It was an unusually mild but blustery morning when I arrived at the kiln at 5.30am. Stillman and his brother Leavitt had taken the night shift, which ran from midnight until then. Their job was to maintain a reducing atmosphere in the kiln and not worry too much about heat gain: by limiting the amount of air entering the kiln, oxygen is pulled out of the pots and glaze materials. There still needs to be enough oxygen for the wood to burn, though, so it's a tricky balance of blocking the kiln up whilst not letting it stall out. Reduction tends to make for nice deep colors rather than pasty ones.
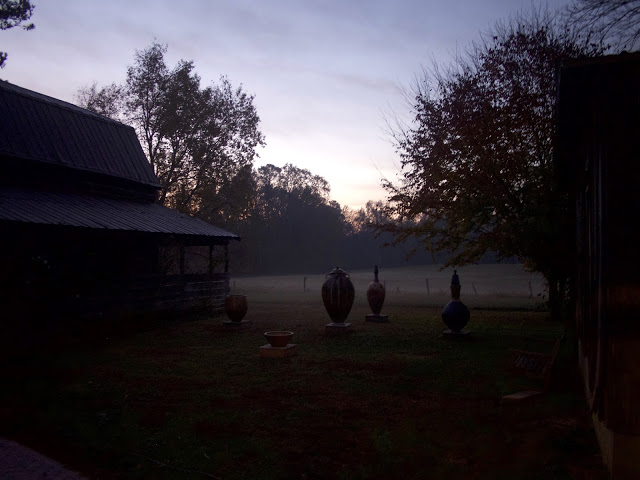 |
Daybreak at the pottery |
When I arrived the pyrometer read about 2100
°F. Black smoke emanating from the chimney and piles of ashes halfway down the kiln suggested that the boys had done a good job. Side stoking helps to keep the reduction throughout the kiln rather than just up at the front near the firebox. Mark and I took over whilst the brothers Browning-Howe went off to nap. We continued reducing for a few hours before opening the air up some and going for temperature gain.
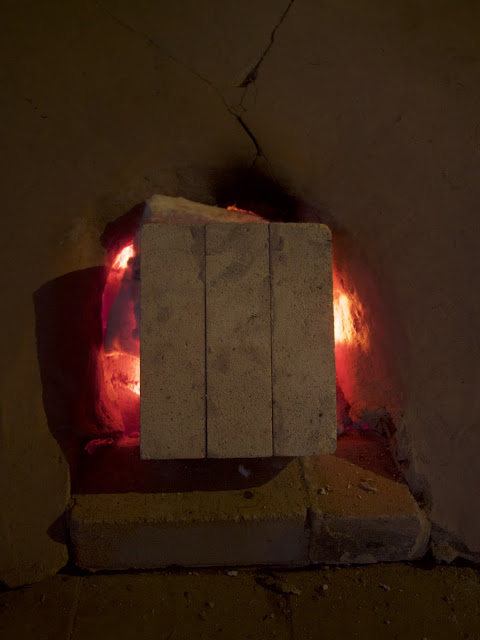 |
Early glow from stoke hole 1. |
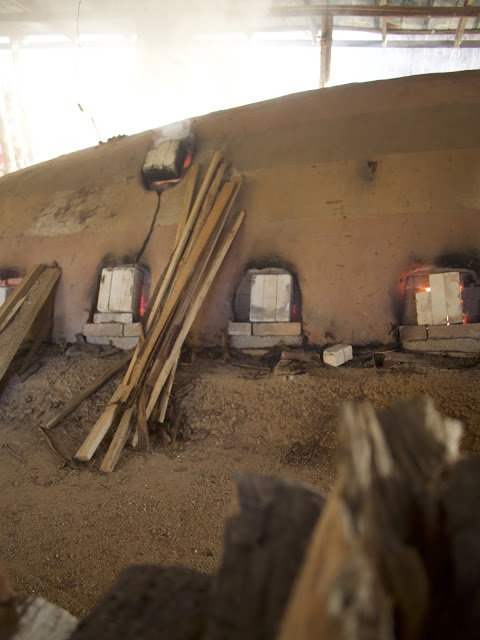 |
Stoking wood prepared, resting on the kiln. |
It took us a while to get the cones moving, but once we did the progress down the kiln was pretty fast. By midday we had a full team out helping. Joe Sink in the firebox, Matt Hallyburton and I side stoking one side, Mark and Stillman working the other. We had to be vigilant watching for sparks or lit leaves flying around as the wind was quite strong. Nothing calamitous happened but the conditions were potentially dangerous.
 |
Joe stoking the firebox around midday. |
By 3pm we were salting the kiln, catapulting 150lbs of salt throughout the kiln with a leaf blower. By 4pm we were opening up the stoking holes to crash cool the beast and peek inside at the orange glowing pots. This crash cooling helps the glazes set and avoids any crystallization. By about 6pm we clammed up all the stoke holes and set to waiting.
 |
Buckets of clamming (a mix of floor sweepings, clay, and sand) with which we seal the kiln. |
 |
Early on in the firing (top picture) and right at the end when we opened up to cool fast (bottom picture). |
A week goes by whilst we bite our nails.
Here's a picture of the vegetable garden in the frosty early morning to provide a little pause here. Its not a great photo so you probably can't tell all thats in there: garlic, rapini, winter peas, buckwheat, rye, collards, sprouts, broccoli, cauliflower, beets, chard, lettuce, kale, tat-soi, turnips, carrots and I'm sure to be forgetting something.
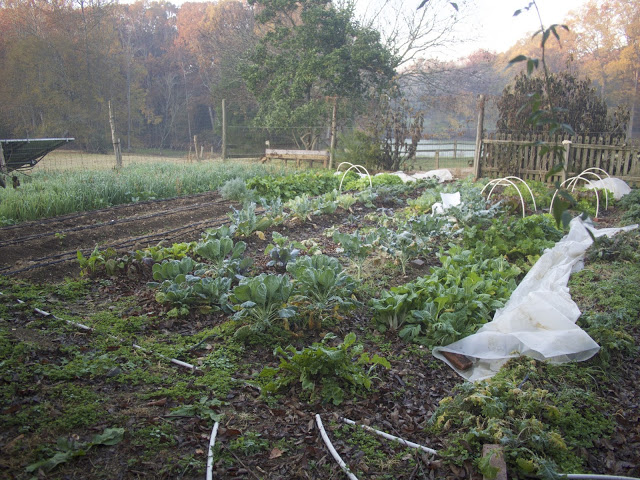 |
The plastic sheeting is to cover tender buttercrunch and other greens from the frost. |
Opening the kiln was a pleasure. We got it nice and hot, and reduced, front to back. The ash glazes came out deeper and more golden than I have seen in my year-and-a-half at the pottery so far. The EPK slip was dark and ate up the salt nicely, and we got lots of wood ash drips at the front. Our new glaze made from local granite was a bit of a mixed bag; it looks fantastic when really hot, but matte in cool spots. Now we know for the future and can pack accordingly. It was an excellent firing; Mark said it could be one of the best ever. So, like a vintage of wine, we shall remember 96 as one of the rather fine ones. Below are pictures of some of the pots on the first morning of the kiln opening. Enjoy.
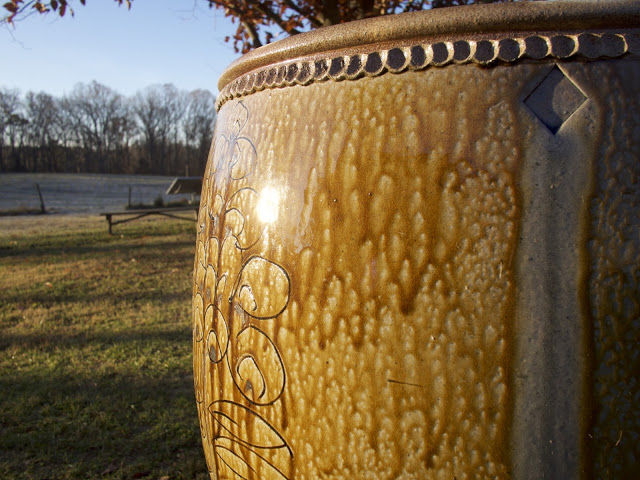 |
Mark Hewitt 120lb planter, 2016. Close up of the ash glaze over incised floral decoration. |
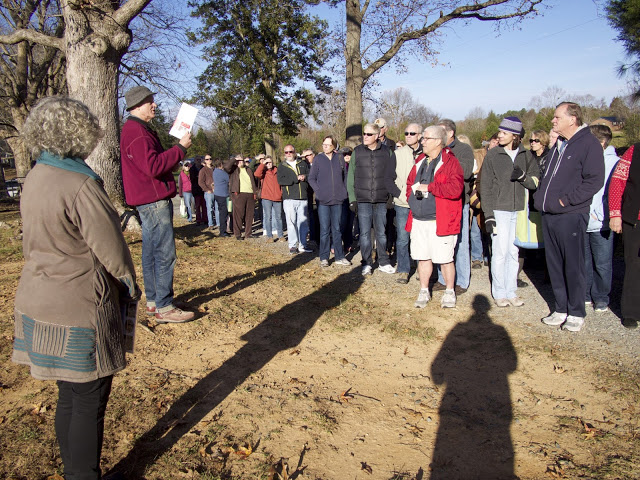 |
A few announcements before letting in the customers this morning. |
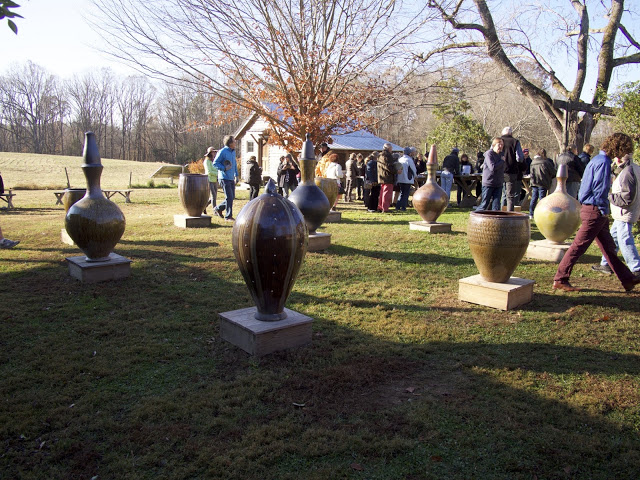 |
The remaining big pots (some had already sold). |
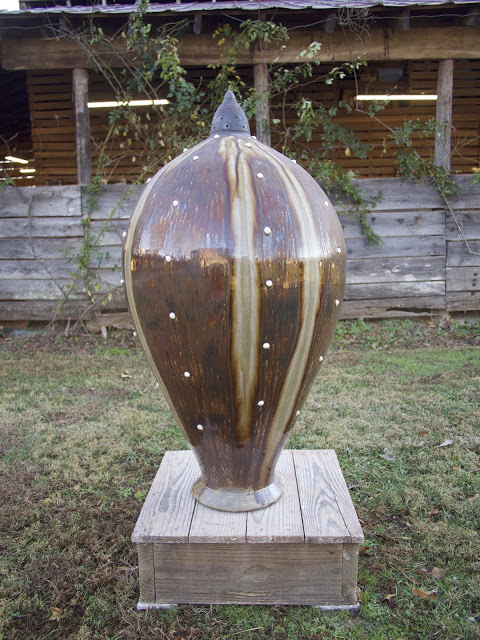 |
Big pot, Mark Hewitt. Ash glaze over manganese slip with glass drips. |
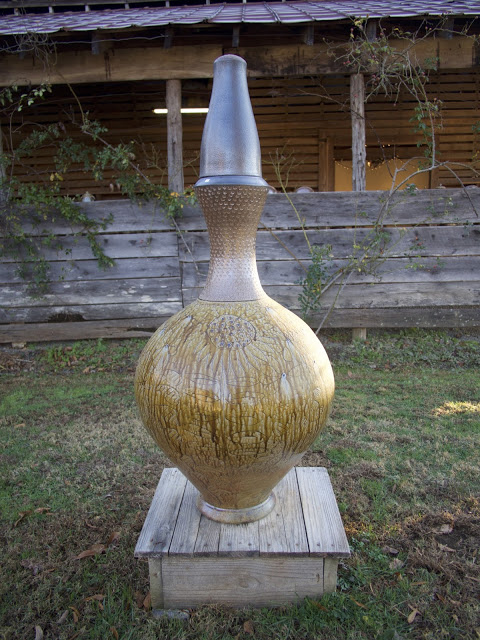 |
Big pot, Mark Hewitt. Ash glaze over incised floral motifs, stamped neck, manganese slip finial. |
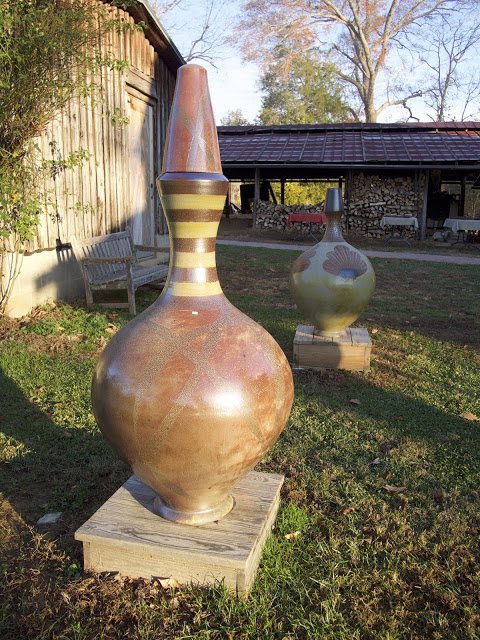 |
Big pots, Mark Hewitt. Mixture of lilac slip and yellow glaze decorations. |
 |
Close up of the neck on one of Mark's big pots; ash glaze with glass decoration. |
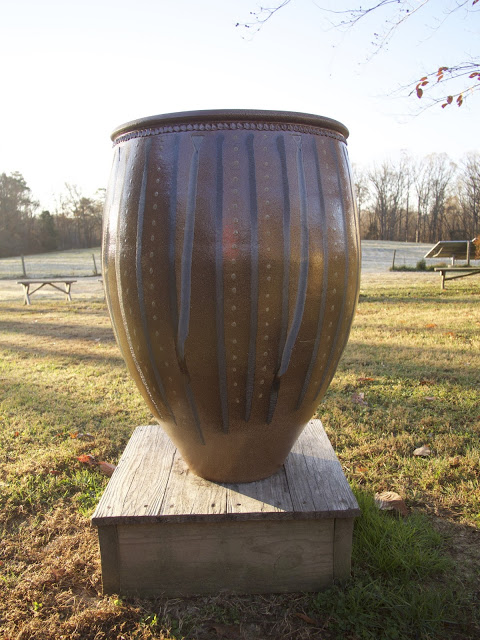 |
Monster planter, Mark Hewitt. Manganese slip lines, white glaze dots, and glass runs. |
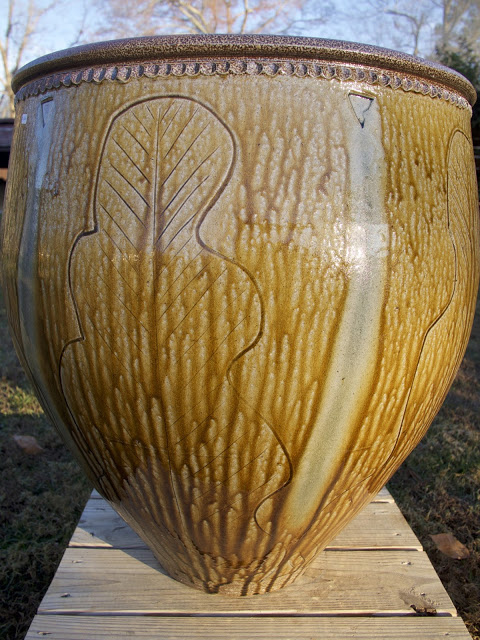 |
Ash glaze 120lb planter, Mark Hewitt. |
 |
Considering a large platter. We fired these underneath the main stacks of pots: some got covered in ashes |
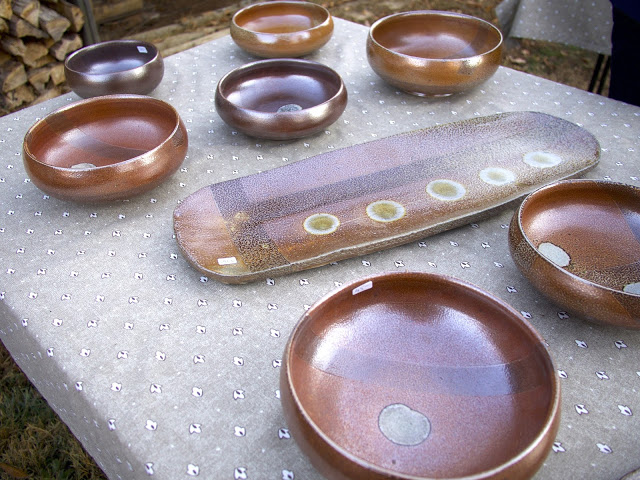 |
These pots were simply slipped and accented with glass. The salty atmosphere of the kiln made them shine! |
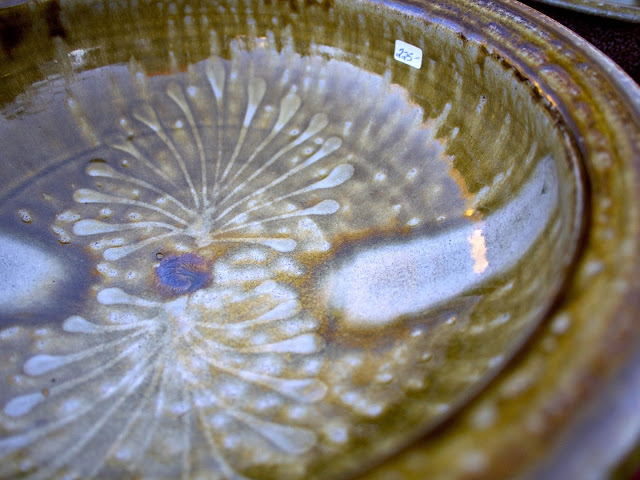 |
Close up of one of Mark's bowls: there is a really beautiful quality to this glaze. |
 |
One of Mark's ash glazed cereal bowls. |
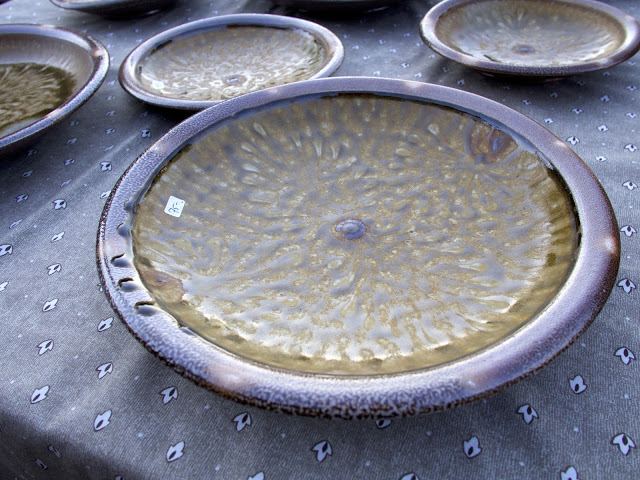 |
Sweet plate-- I like the drips peeking out over the rim. |
Into the inner barn...
 |
Mostly ash/alkaline glazed pots by Mark. |
 |
10 gallon vase, Mark Hewitt. Ash glaze over incised zigzagging lines, blue glass on shoulder, manganese slip neck. |
 |
Grave markers, Mark Hewitt. |
 |
Canister jar, Mark Hewitt. EPK slip. |
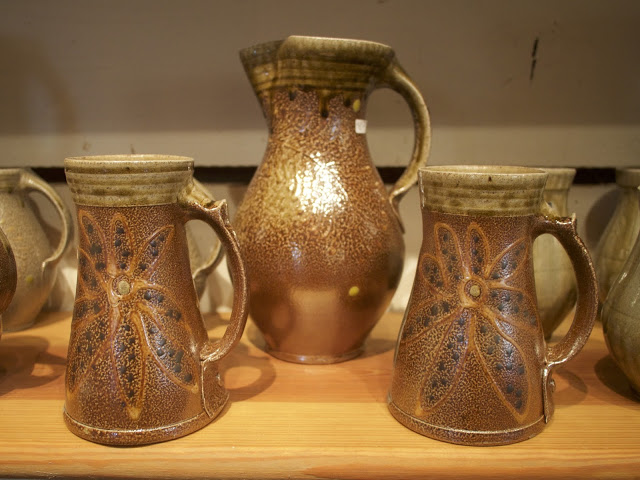 |
Tankards (and pitcher), Mark Hewitt. Slip trailed decoration. |
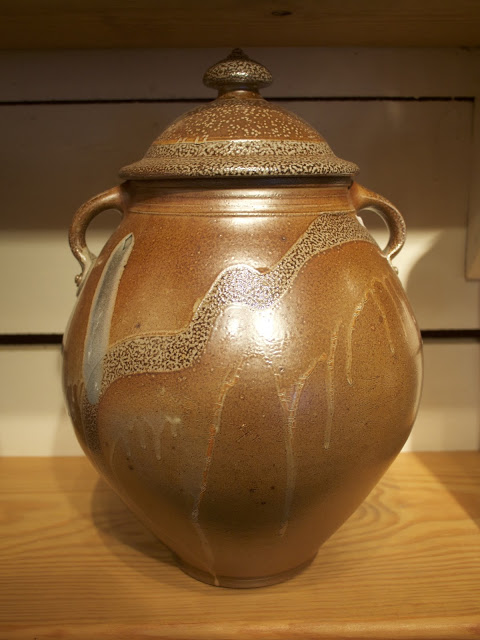 |
Cookie jar (7lb), Mark Hewitt. EPK slip. |
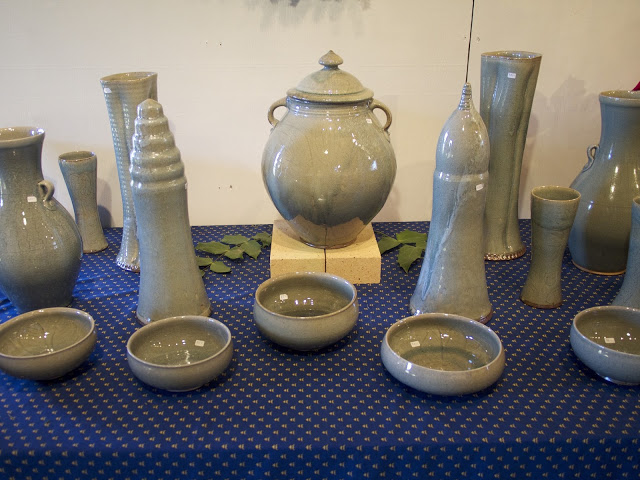 |
Various of Mark's pots with our new local granite celadon. |
And now some of mine and Stillman's pots...
 |
A couple of shelves of my pots. |
 |
Tumblers. Stillman Browning-Howe. Slip trailed decoration.
|
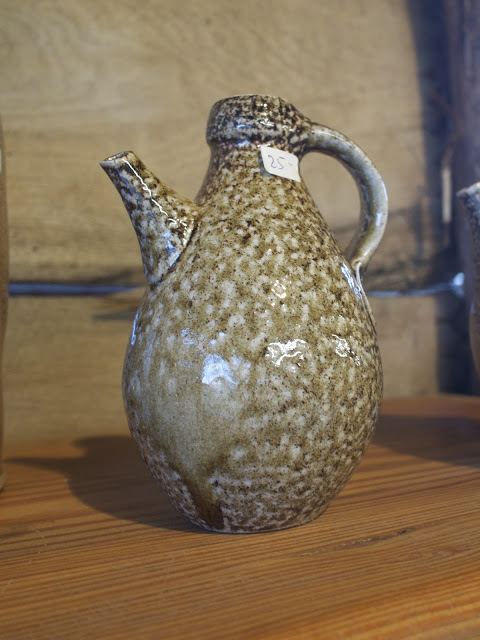 |
Small 3/4lb cruet, Hamish Jackson. I am really into these; definitely have to make more next time. |
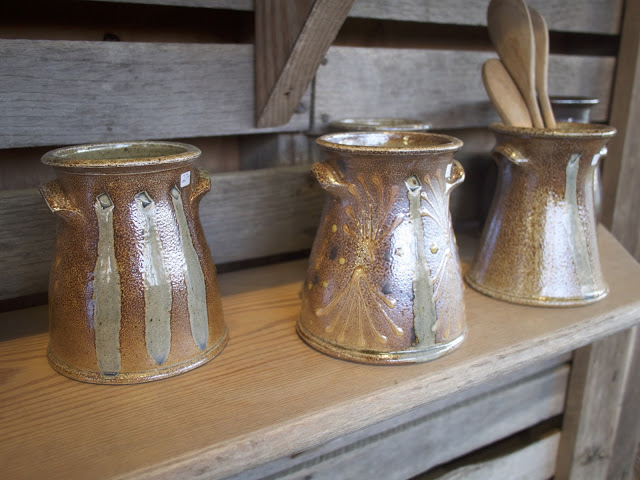 |
Spoon holders, Hamish Jackson. |
 |
Teapot, Hamish Jackson. My first teapots at the Hewitt Pottery! My favorite things to make by far... so much to go wrong but I love them. Mark is very particular about them too: they have to be light with low bellies, high handles, and sharply upturned spouts.
|
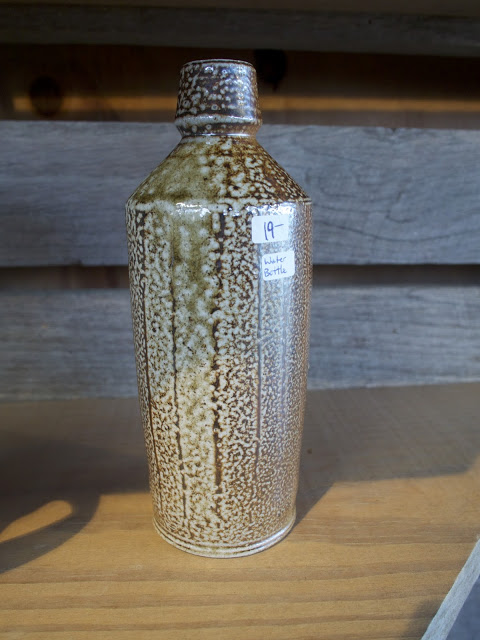 |
Water (or beer) bottle. Hamish Jackson. |
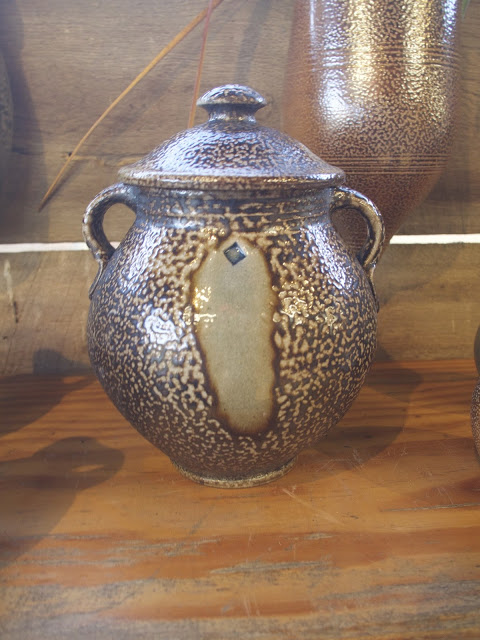 |
Cookie jar, Hamish Jackson. Black slip dimpled by heavy salting with blue glass drip. |
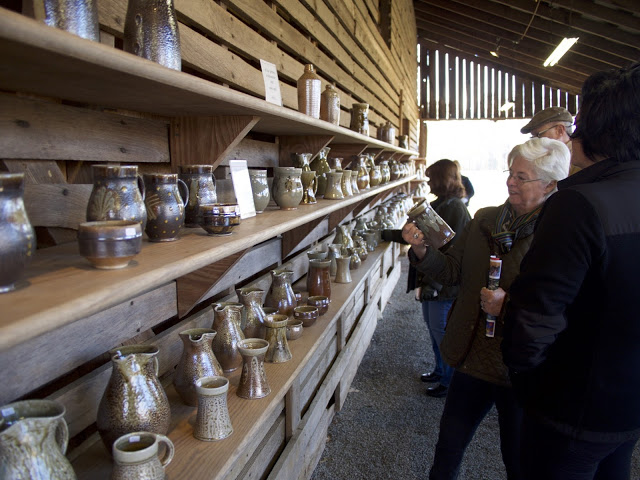 |
Considering one of my tankards. |
 |
Tankard, Hamish Jackson. My first attempt at doing these curly handles -- quite fun.
|
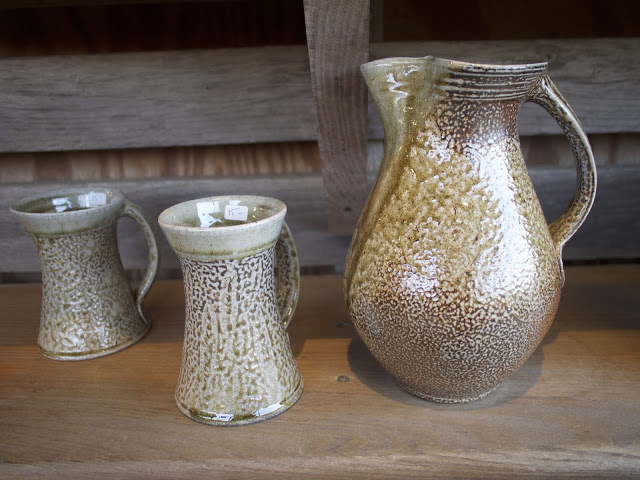 |
One of my pitchers and a couple of mugs. I am not happy with the shape of any of these, really, but especially not the pitcher; it needs a fatter belly, and a tighter, longer neck. |
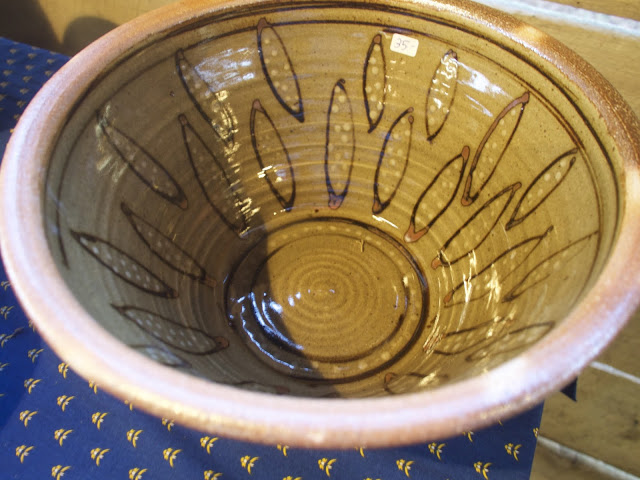 |
Mixing bowl, Hamish Jackson. Slip trailed decoration. |
 |
Wall vases/pockets, Hamish Jackson. I like making these; especially as they remind me of bees. |
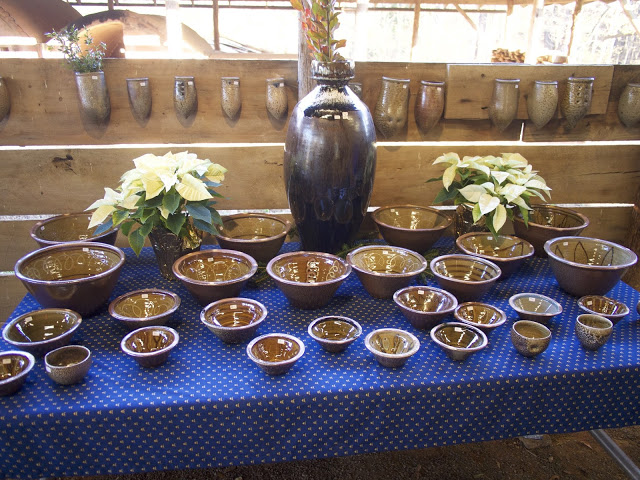 |
Some of mine and Stilly's mixing bowls.
|
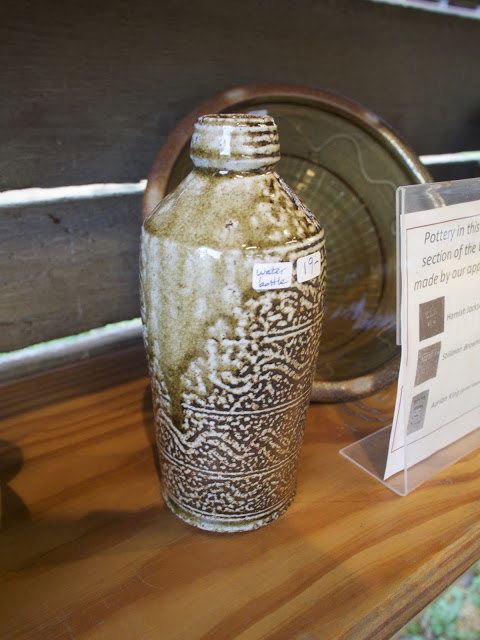 |
Bottle, Hamish Jackson. Nice firing on this bottle: plenty of salt and lots of wood ash collected on the shoulder which melted down. |
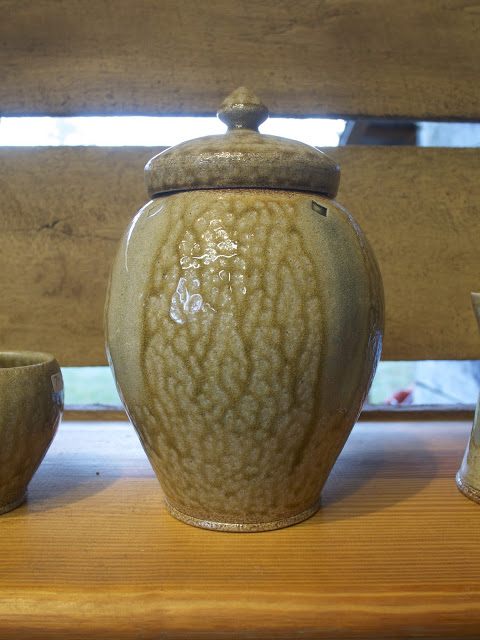 |
Ginger jar, Stillman Browning-Howe. It was great watching Stilly get into making his first ginger jars; his enthusiasm is infectious. Some of them, like this one, came out really nicely. |
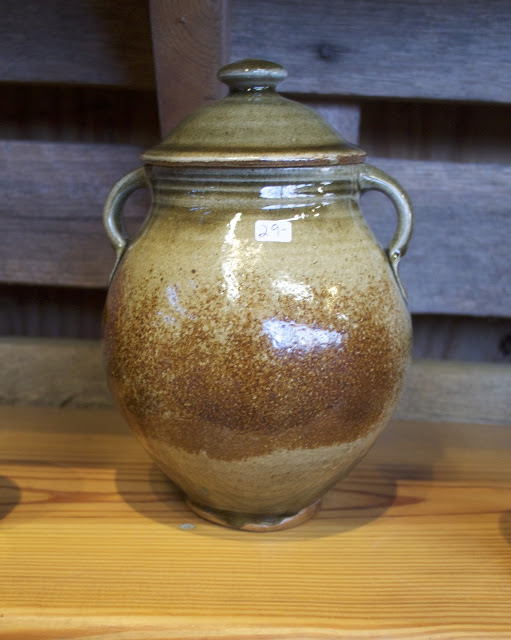 |
Cookie jar, Hamish Jackson. This was glazed with our granite celadon + 1% ochre. |
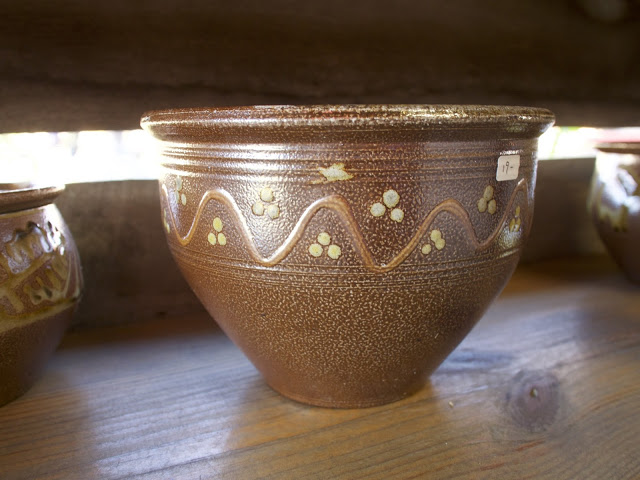 |
Flower pot, Hamish Jackson. Slip trailed decoration. |
 |
Much interest at this table -- some bargains to be had. |
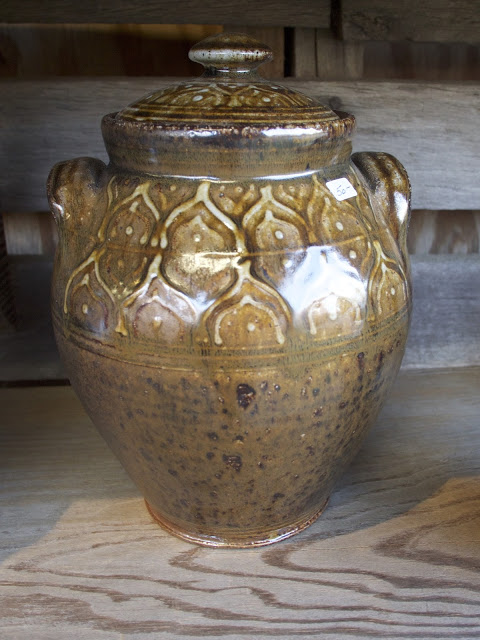 |
Jar, Adrian King (former apprentice); still up for grabs! |
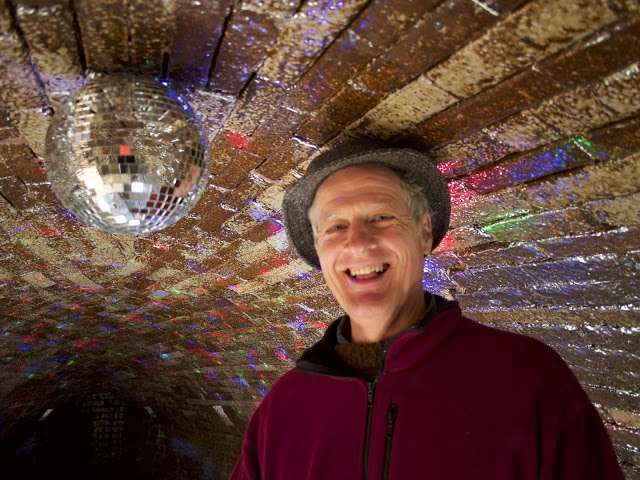 |
Mark rockin' out in the kiln. We put a disco ball up for all those who needed a break from the riotous christmas shopping. |
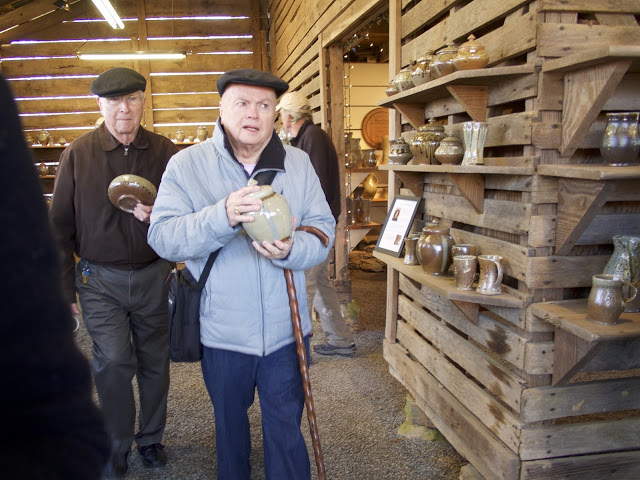 |
Nice chap clutching one of Stillman's jars and heading for the checkout (or the disco kiln?). |
 |
This lady came prepared with not one but two baskets. |
 |
96 done. |
Roll on 97.