Chun (jun) glaze initial tests
I have long admired chun glazes and dreamed of trying to create my own version with materials I collect locally. Three months before my thesis show in grad school seemed like a perfect time to start in earnest haha.
To begin the search I read up on chun or jun glazes from some of my favorite books.…
I also found the website Glazy very useful. I was able to take the analysis of Chinese chun glazes from the Song period (in Nigel Wood’s book) and target the composition using my locally collected granite.
I recently got my granite analysed by a wonderful lab at Washington State University. They took my granite, ground it up and ran it through an x-ray fluorescence machine. Normally it costs $120 a sample but as a student at a research institute I got each for $60. You have to post the samples to them too but they prefer to do all of the grinding. They just need more than 100 grams of the rock to analyse. I sent extra just to be safe.
You can read more about this and see the full analysis of my materials in this blog post.
Glazy is also helpful for the recipes on it already. I went through, compared them all and this helped me get an idea of where the chun zone was too.
I used glazy to target the Unity Molecular Formula of several song dynasty chun glazes from Nigel Wood’s book, and then also some others I found online from David Fry, Derek Au, Harlan House and Atelier Aimee. I basically tried to achieve the same UMF but using at least 50% of my granite from Devil’s Playground, Utah.
I tinkered around for a while on glazy and came up with 12 possible chun glazes. I mixed up 100 grams of each, weighing out he ingredients carefully and adding 55ml of water to them. I sieved each twice and then dipped 4 test tiles in each, to be fired in different ways. I also dipped one large extruded test tile in each (in a trough): I like these larger tiles for seeing what happens on a larger surface but they do not tell you how runny the glaze will be.
Here is the first set in the kiln, fired to cone 10. Cone 11 is still standing there.
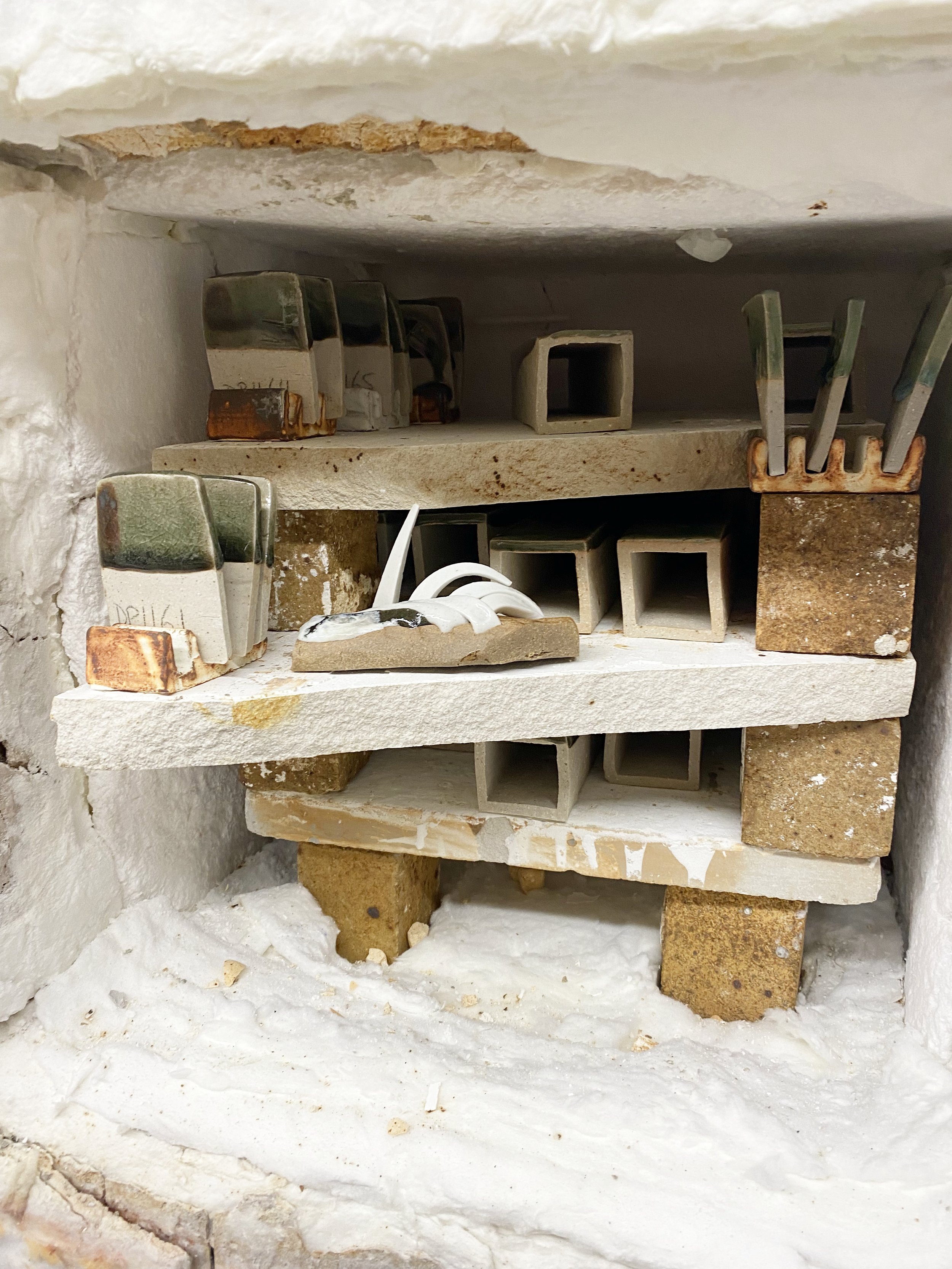
Initially I was disappointed upon examining the tests. I was hoping for a varied line up of chun glazes. See my last post for some pictures of what I was hoping for. Not this haha. These look very much like celadons of various shades. However, upon close inspection I could see the beginnings of chun effects… the beginnings of liquid-liquid phase separation, and of bubbles clouding the surface.
Here is a closer look at each of the tests, with their recipes…
DP1160 (you can see the chun effect starting a little here where the glaze is thickest):
DP1161:
DP1162:
DP1163 (I knocked the glaze off this tile on the way into the kiln so the small test tile is not a good representation of the glaze):
DP1164 (you can see the chun effect starting a little here where the glaze is thickest):
DP1165 (you can see the chun effect starting a little here where the glaze is thickest):
DP1166 (you can see the chun effect starting here where the glaze is thickest):
DP1167 (you can see the chun effect starting where the glaze is thickest):
DP1168 (you can see the chun effect starting a little here where the glaze is thickest):
DP1169. The last couple of pictures show DP1169 fired to cone 11: much less crystallized. This glaze matted out because of too much magnesium I think: this comes from both the talc and dolomite.
DP1170 (you can see the chun effect starting a here where the glaze is thickest: nice color!):
DP1171 (you can see the chun effect starting a here where the glaze is thickest):
Here is a broad view again but this time with the same tiles fired to cone 11 underneath. As you might expect the glazes ran more, but also I saw less chun effects.
IHere are the cone 11 tests closer up (the ones off the wooden board)…
In the literature there were some hints that higher temps aided the chun effect but I did not find this-at least not with these formulations. Maybe with stiffer, more silica rich glazes this may prove true. I will continue to test to cone 11 but it seems like cone 10 in reduction is the ticket.
Overall I was encouraged by the cone 10 tests. I did not achieve a chun glaze but there were hints of phase separation, and the formation of bubbles. I was also encouraged by the color of the copper carbonate, applied under the glaze. I just love the old song dynasty chun glazes with purple sashes. Research from various sources has confirmed this was copper applied sometimes under or over the glaze. I tired it out in the hopes that it would work and was surprised to see that it did.
After going back to the drawing board and reading through my notes again I think I figured I should try pumping up the silica content in the glazes. I plan to do an Ian Currie style grid to give myself 35 glaze combinations in short order… hopefully that gets me closer to a chun.
Hope springs eternal!
REVISION:
Since writing this blog post I have tested these same 12 initial tests in a much more reduced firing (gas firing 6), with an intentional reduction down firing. The results were pretty similar I’d say. Here they are…